by Shane Dunstan | Dec 20, 2021 | Civil, Dams, Environment, Mixing, New Technology, Pavements, RCC, Upgrading
The original mobile continuous mixing plant now made in North America!
The Aran Mobile Plant is back, and with our new North American Series, it’s bigger, tougher and better than ever. We’ve used 45 yrs of experience to design and build for your local conditions and standards.
The new Aran Environmix Mobile Mixing Plant is different. It’s designed and built in North America. It’s tougher and stronger than ever before, ready to take on any job. We might be biased, but we believe this is the best Aran machine yet!
Looking at getting into the mixing business, upgrading to a new machine or exploring switching to a better brand, get in contact to learn more about why we believe this mixing plant is the right investment for your business.
Aran Environmix Product Brochure
by Andie Vandenhul | Sep 6, 2019 | Civil, Dams, Environment, Mining, Mixing, New Technology, Pavements, Quarry, RCC
Without the past what would we become?
Whilst searching the archives of Aran’s technical papers this week we located a transportation planning study for Brisbane City, published in 1965. The insights into population growth and infrastructure development demands were surprisingly accurate.
Planned projects, costed to pounds and pence, with grade and alignment designs, many of which have been constructed in various forms. Some are still needed. Some abandoned for the preservation of urban lifestyle. It was fascinating to reflect on Aran’s contribution to the development of Brisbane’s road network for over 40 years. Click the pic for the 2004 Program.
Click Here for the Full Oral History Report.
This interview is an excerpt from a Report which was commissioned by the New South Wales State Road Authority (RTA Roads and Traffic Authority) in Australia. This report was commissioned in 1997 to investigate various topics, based on 28 hours of digitally recorded interviews from 23 participants. Trevor Dunstan, Aran Founder, was interviewed to talk about the introduction of mobile pugmills.
Today, Aran’s legacy has been paved around the world and continues to be a reliable contributor to the world’s building infrastructure.
by Andie Vandenhul | Sep 2, 2019 | Civil, Dams, Environment, Mining, Mixing, New Technology, Pavements, Quarry, RCC
Aran Mixer Effectiveness Index History and Report
The history and origination of the Continuous Mixer began in the mid 1980’s.
Aran was founded on a solid focus of excellence in engineered solutions. This is not only apparent in the robust design of the equipment, but a collaborative scientific approach to developing industry standards and construction methods. One example of this is the development of a rationale and equation to objectively measure the effectiveness of mixer types for mixing cementitious materials.
1985, Dutch Stephenson, founder and owner for Stephensons Construction of Washington, bought the second Aran ASR200 mobile pugmill to be used in the USA. Dutch was a pioneer in mixing RCC and CTB, with his first project at the Burlington Northern Railroad in Denver. RCC was still in its infancy in 1985, with some contractors attempting to produce RCC with inadequate equipment. Some projects were poorly completed. It was necessary to prove that the Aran pugmill and material metering feeders had the accuracy and mixing effectiveness necessary to produce a quality RCC mix. Collaborating with Aran and the Portland Cement Association (PCA) Stephenson tested the Aran pugmill in Tacoma, WA with several mix designs. The testing proved the Aran plant could not only produce RCC, but also various traditional designs of slump concrete. Stephenson raised the challenge to Aran to develop a plant primarily focused on Concrete.
In 1986 Aran released the ASR280C (C for Concrete) mobile pugmill. This machine included many new features to improve its capability of material dosing and mixing concrete. These features included a larger cement metering feeder with negative pressure silo, improved aggregate hopper and metering feeder and most importantly, the mixer with a new blade phasing arrangement and various other flexible operating features. To prove the new design Aran invested in ~$300,000 testing program at the Monnier Hard Rock Quarry in Redbank, QLD Australia. Construction Testing Pty Ltd of Brisbane were engaged in June 1986 to test materials produced by the new Aran ASR280C pugmill. The results were also reviewed and ratified by Golder Associates.
Testing included the following samples:
10-30mpa Pavement Type Concretes to assess the following plant performance metrics:
- Consistency of mix over time, collecting material at 40 second intervals from the start to the end of a production cycle (Batch).
- Consistency across the mixer and discharge belt from batch to batch. Samples taken at the centre and each edge of the static belt.
- Consistency – short run reliability of mix at 15 second and 30 second batch run intervals.
- Air Entrainment evaluation with samples taken at 10, 20, 30 then 15 sec intervals over 90 second total sample production runs, at 10-30mm slump and 50-60mm slump.
- Water Reducing agent evaluation with the same intervals.
A large database of records collect confirmed that Aran ASR280C:
- Demonstrated uniformity of cement feed, whilst the silo was being filled and at various levels.
- Demonstrated sufficient mixing time and mixing thoroughness by material testing and using colour additives
- Demonstrated effectiveness of admixtures
- Slump uniformity
During the trials, Aran tested several mixing blade phasing patterns, blade angles, mixer shaft speeds and entire mixing chamber angles. Some adjustments to mechanical or operational characteristics made very little difference, others made a significant difference in mix quality.
On the strength of these positive test results, Dutch Stephenson ordered another Aran machine, an ASR280C delivered in September 1986.
These testing program results aroused elevated interest in the unique Aran pugmill design and its capacity to produce high quality product, at high instantaneous production rates. It was important to prove the Aran pugmill credentials, differentiating it from other mixing systems traditionally employed.
In October 1986, Trevor Dunstan developed, what is now known at the Mixer Effectiveness Equation or Mixer Effectiveness Index (MEI). Written as an appendix to his white paper titled “Continuous Volumetric Metering of Concrete Ingredients, The Aran Equipment Approach to Accuracy – How it Works”. This paper was presented at various conferences and industry meetings in Australia, USA, China and Europe during the remainder of the 1980’s and early 1990’s. The MEI was later updated in 2006 to include other input data necessary to give a reliable measure for applications when mixers are processing slurries and clays. The original Mixer Effectiveness Index is still used by many designers and contractors today.
by Shane Dunstan | Feb 9, 2016 | Pavements, Upgrading
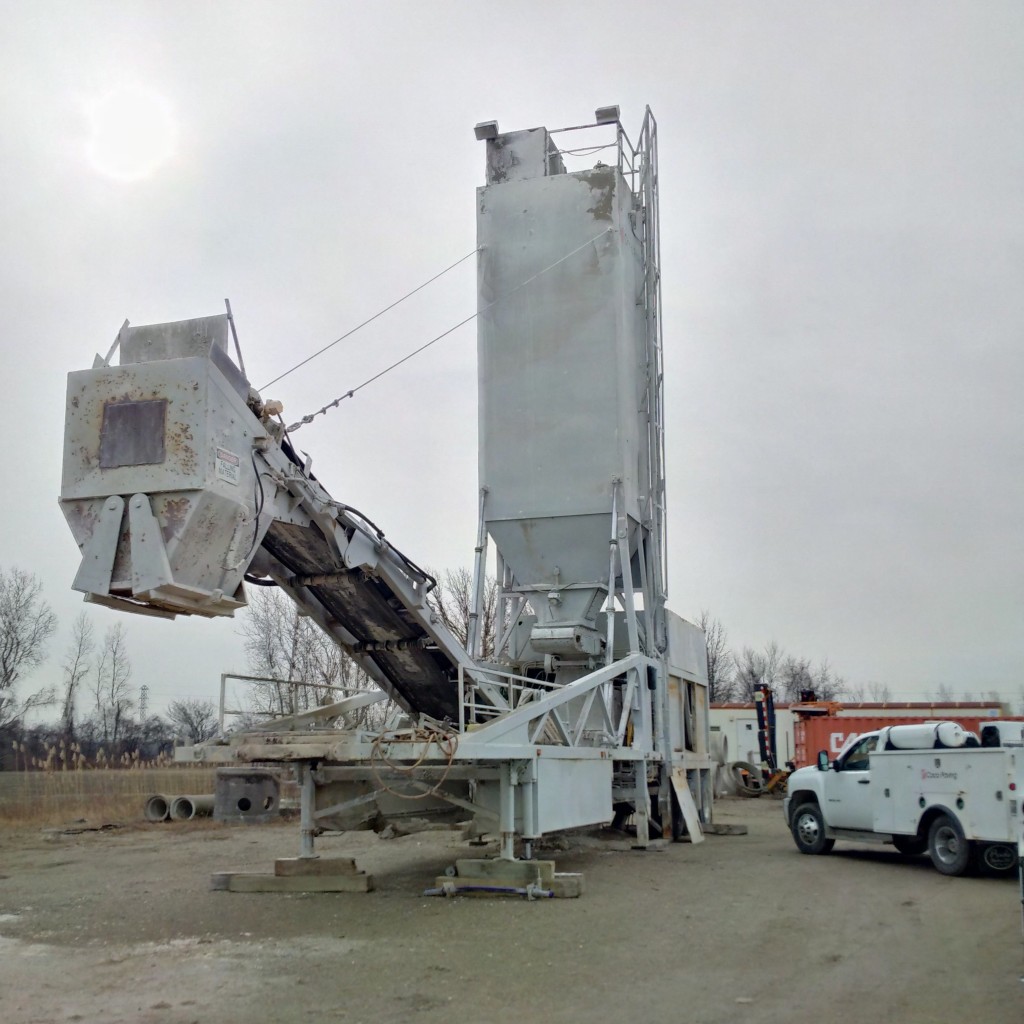
Winter Maintenance Time.
Inheriting equipment as a result of M&A presents new challenges to plant and equipment departments. Hear how Aran focuses on developing strong relationships with machine owners to help them achieve successful outcomes in terms of maintenance and operation of inherited equipment.
Windsor ON Canada pavement construction company, Coco Paving, has an ever growing business and equipment fleet. As a result of acquiring other construction companies in the region, Coco inherited an Aran ASR280E series mobile mixing plant a few years ago.
The ASR280 mobile mixing plant is a key component of Coco Paving’s asphalt production. Quarried materials sourced for many of Coco’s projects require the addition of lime (1%) prior to use in its asphalt plants. Without the accurate addition and homogeneous distribution of lime, the production of a successful pavement would not be possible. Producing 150,000 tonnes conditioned material each construction season requires the mixing plant to be operated up to 5 days each week, often for double shifts to meet project demands. This level of equipment utilisation limits opportunity to service and maintenance.
During a recent visit to Coco Paving’s maintenance facility Aran performed an informal equipment audit ahead of the next construction season. When major maintenance is restricted to one period per year (winter), the extent of the work required can be significant. It is not uncommon for some plant operators to focus on pushing material through the mixer towards the end of the project or season and sacrifice the condition of the mixer. Thus, mixer effectiveness, efficiency and the resulting mix quality and energy consumption are compromised.
To their credit, the maintenance team at Coco have been thorough and resourceful. Whilst their familiarity of the machine was initially limited, with Aran’s help, they have are coming up to speed with the function of the plant and areas of the plant requiring attention.
This winter (2015/16) this machine is receiving a full engine and mixer rebuild.
Aran has assisted Coco with the replacement all major components for mixer, including new shafts and wearing components, special housings and delivered recommendations for other system service.
We always want to learn from Aran machine owners, operators and maintenance teams. Learn about their experiences on the job, in the workshop or at the boardroom table. We have a lot to learn and a lot of experience to contribute.
As an owner of an Aran machine, you not only have the support of a committed and experienced team, but a network of passionate and skillful operators.
If you have an operational or maintenance challenge with your mixing plant, get in touch. We’d like to connect with you and help you achieve the very best from your equipment and projects.
Tell us about your story!
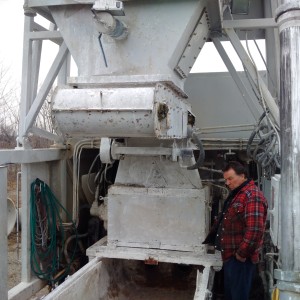
Full Mixer Refurbishment and Silo Feeder Service
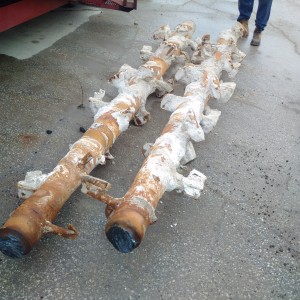
Often it is more efficient and cost effective to replace mixing shafts during heavy maintenance.
by Shane Dunstan | Apr 27, 2015 | Environment, Pavements, Upgrading
See how equipping for growth early will cement your position as an industry leader.
Boral Recycling use an Aran Modumix mixing plant to deliver pavement construction materials to Sydney projects with a solid respect for the environment.
Western Sydney is the recycling center for Australia’s largest city. Receiving many thousands of tonnes each day of old construction materials from building and pavement demolition sites, Boral will crush, screen and stockpile materials for reuse. These processed materials are later delivered to new projects either as fill or stabilised road construction material. The Aran mixing plant is a key to the success of this business.
Road construction specifications require very accurate dosing of binders and water to produce a constructed pavement with consistent density and strength. This can be challenging to achieve with recycled materials containing residual cement. Boral elected to install an accurate, high production mixing plant in 2008 to service the rapidly growing need for recycled material in Sydney and beyond. Considerably larger that what was needed in 2008, Boral identified the growth in Sydney would demand a high production plant for the future and purchased a second hand Aran Modumix II modular mixing plant. With a proven history of mixing large volumes of material very accurately, this was the perfect choice for Boral. In years prior, this mixing plant, along with an identical twin plant, produced over one million cubic yards of Roller Compacted Concrete for a dam in South Carolina, USA. Prior to installing the plant in Sydney, Aran refurbished the machine, including the installation of a new control system and a third silo and metering system.
I recently visited this machine just after its 13th year, with 7 years operating at Boral’s facility in Sydney. This machine is operating every day, producing material at rates of 420 cubic meters per hour or greater, with binder contents of 0-11 percent. The accuracy of the cement metering is an impressive 0.033% variance across milestone targets. This is easily within the specified guidelines and a good example of the Aran SiloFeed system to perform on a 13 year old machine. This accuracy gives clients confidence they are receiving a quality product and Boral the confidence that they are not only producing a product on specification, but doing so efficiently.
High production rates is not only geared for processing orders for material quickly, it also allows Boral to charge trucks very rapidly and maintain a clear traffic flow around the plant. Speed and efficiency helps this site run smoothly and successfully.
Learn more about how Aran can help you attract more customers along with improving: your production rates and efficient use of material. Get in touch and tell us your story.
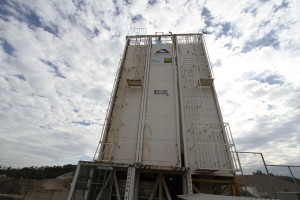
Three potential binder blends give Boral the flexibility to meet demanding project specifications.
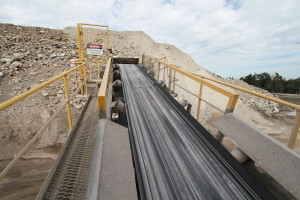
High rates of production + fast truck charging and efficient operations.
by Shane Dunstan | Apr 11, 2015 | New Technology, Pavements
Philippines is a rapidly developing nation with many thousands of kilometers of road pavements to construct and maintain – testing climatic conditions, increasing traffic and punishing heavy vehicle loads result in premature pavement failures.
With a lack of available space and time permitted for road closures, Roller Compacted Concrete (RCC) pavements present a compelling solution to the reconstruction of failed pavements and RCC can also meet the need for new pavements to be constructed quickly, cost effectively and opened quickly to traffic.
Following the many applications of RCC pavements in North America, Cemex Philippines has introduced the innovative pavement construction technology to the Philippines. After a comprehensive study in 2014 of materials, construction process and equipment used for RCC, the first test pavements have been placed in greater Manila, April 2015.
A new Volvo ABG paver and Aran mixing plant where selected to be the cornerstones of their RCC business. This is an equipment partnership which extends back to the early 1980’s when Aran and ABG equipment was used first for soil cement and RCC in Australia and the United States.
The Aran modular mixing system used for producing the RCC in the Philippines is based on well proven technology employed over 25 years ago and still constructing the majority of the RCC pavements in North America today.
The Aran WBS series plant (based on heritage Aran technology) manufactured in Asia, presented Cemex a plant relevant to the commercial environment and capable of delivering accurate material proportioning and mixer performance, critical for RCC.
Cemex are motivated and equipped to expand their business with RCC. Successful construction of RCC pavements demands attention to material selection and gradation, mix handling and logistics, to ensure a densely compacted pavement is achieved.
It is without a doubt, the team at Cemex Philippines have the skills, the commitment and now the equipment to see RCC become a leading construction method in the Philippines.
To learn more about Roller Compacted Concrete and why Cemex chose Aran technology to start their RCC business in the Philippines, get in touch through our contact page.
New Aran WBS300, heritage Aran technology for modern area (image below)
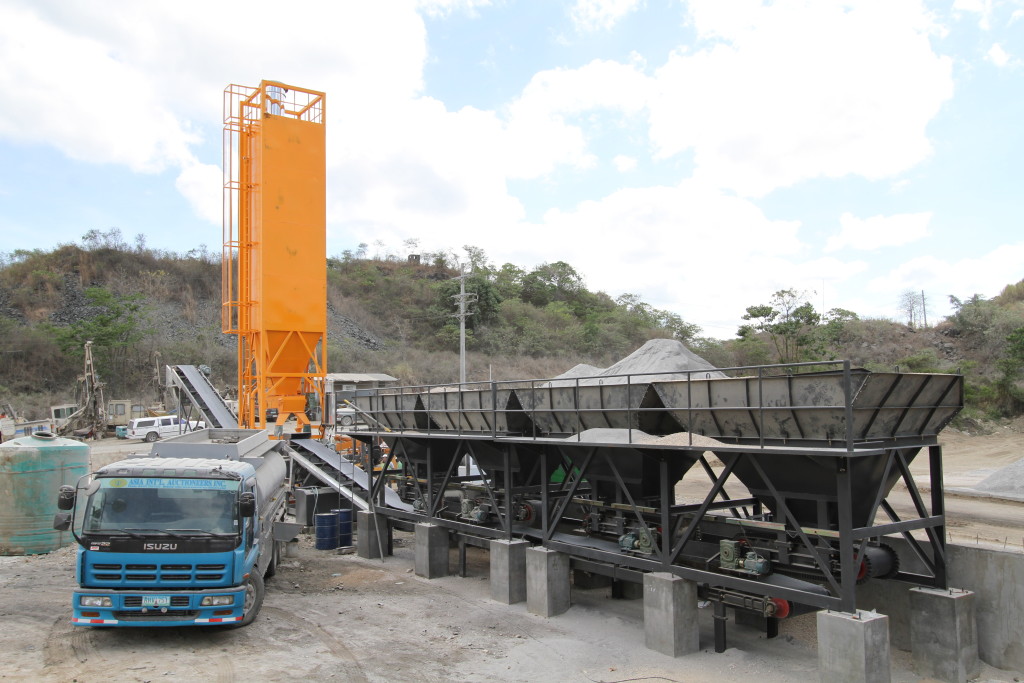
Aran continuous mixer producing RCC
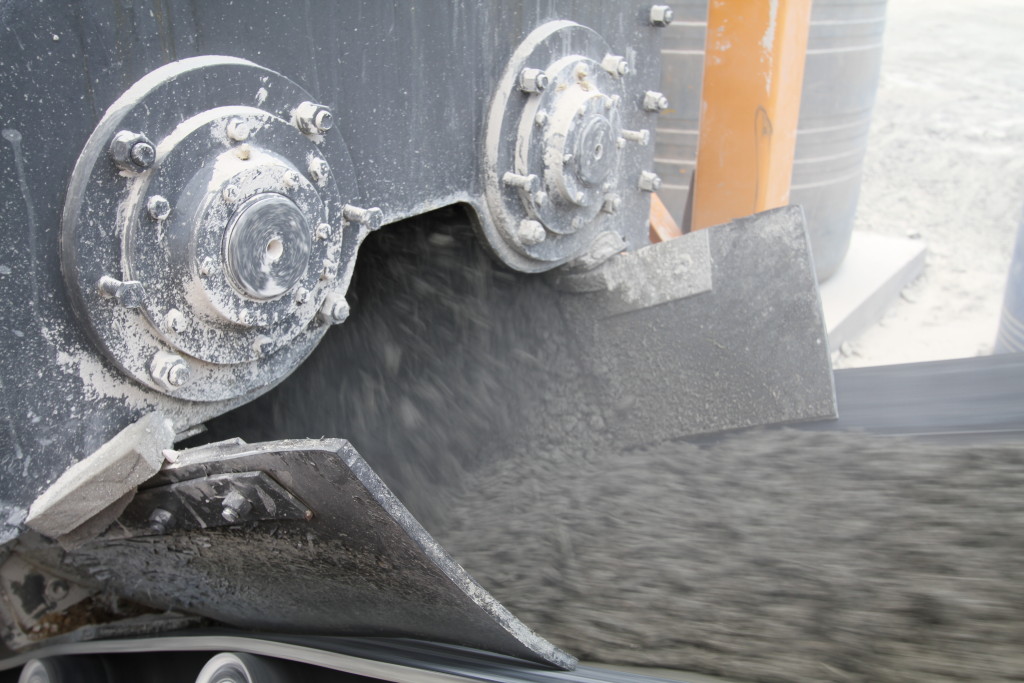
Starting a new run of RCC pavement. Pavement trials in greater Manila, Philippines
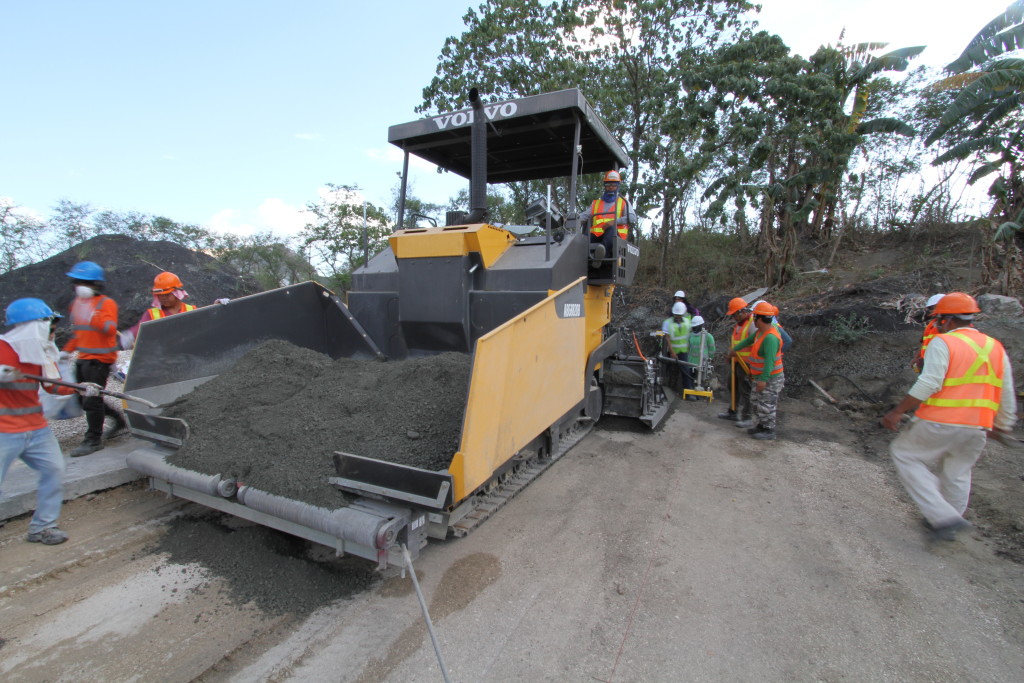
Early RCC Pavement Trial
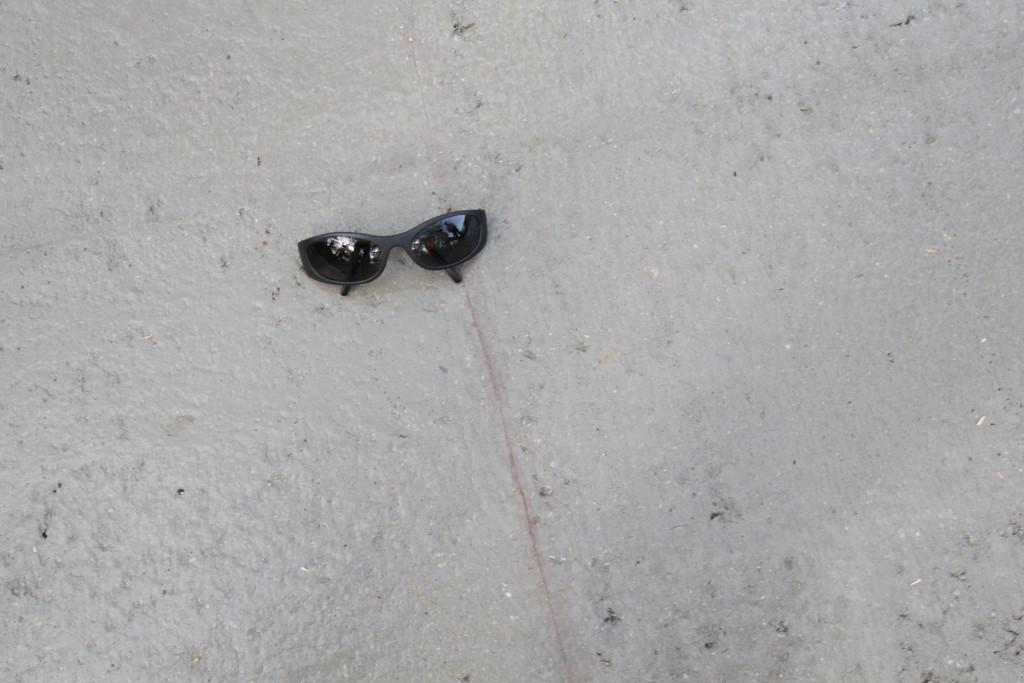