by Shane Dunstan | Apr 27, 2015 | Environment, Pavements, Upgrading
See how equipping for growth early will cement your position as an industry leader.
Boral Recycling use an Aran Modumix mixing plant to deliver pavement construction materials to Sydney projects with a solid respect for the environment.
Western Sydney is the recycling center for Australia’s largest city. Receiving many thousands of tonnes each day of old construction materials from building and pavement demolition sites, Boral will crush, screen and stockpile materials for reuse. These processed materials are later delivered to new projects either as fill or stabilised road construction material. The Aran mixing plant is a key to the success of this business.
Road construction specifications require very accurate dosing of binders and water to produce a constructed pavement with consistent density and strength. This can be challenging to achieve with recycled materials containing residual cement. Boral elected to install an accurate, high production mixing plant in 2008 to service the rapidly growing need for recycled material in Sydney and beyond. Considerably larger that what was needed in 2008, Boral identified the growth in Sydney would demand a high production plant for the future and purchased a second hand Aran Modumix II modular mixing plant. With a proven history of mixing large volumes of material very accurately, this was the perfect choice for Boral. In years prior, this mixing plant, along with an identical twin plant, produced over one million cubic yards of Roller Compacted Concrete for a dam in South Carolina, USA. Prior to installing the plant in Sydney, Aran refurbished the machine, including the installation of a new control system and a third silo and metering system.
I recently visited this machine just after its 13th year, with 7 years operating at Boral’s facility in Sydney. This machine is operating every day, producing material at rates of 420 cubic meters per hour or greater, with binder contents of 0-11 percent. The accuracy of the cement metering is an impressive 0.033% variance across milestone targets. This is easily within the specified guidelines and a good example of the Aran SiloFeed system to perform on a 13 year old machine. This accuracy gives clients confidence they are receiving a quality product and Boral the confidence that they are not only producing a product on specification, but doing so efficiently.
High production rates is not only geared for processing orders for material quickly, it also allows Boral to charge trucks very rapidly and maintain a clear traffic flow around the plant. Speed and efficiency helps this site run smoothly and successfully.
Learn more about how Aran can help you attract more customers along with improving: your production rates and efficient use of material. Get in touch and tell us your story.
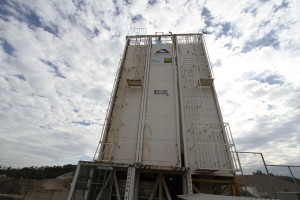
Three potential binder blends give Boral the flexibility to meet demanding project specifications.
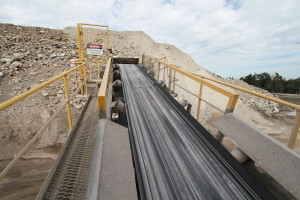
High rates of production + fast truck charging and efficient operations.
by Shane Dunstan | Apr 11, 2015 | New Technology, Pavements
Philippines is a rapidly developing nation with many thousands of kilometers of road pavements to construct and maintain – testing climatic conditions, increasing traffic and punishing heavy vehicle loads result in premature pavement failures.
With a lack of available space and time permitted for road closures, Roller Compacted Concrete (RCC) pavements present a compelling solution to the reconstruction of failed pavements and RCC can also meet the need for new pavements to be constructed quickly, cost effectively and opened quickly to traffic.
Following the many applications of RCC pavements in North America, Cemex Philippines has introduced the innovative pavement construction technology to the Philippines. After a comprehensive study in 2014 of materials, construction process and equipment used for RCC, the first test pavements have been placed in greater Manila, April 2015.
A new Volvo ABG paver and Aran mixing plant where selected to be the cornerstones of their RCC business. This is an equipment partnership which extends back to the early 1980’s when Aran and ABG equipment was used first for soil cement and RCC in Australia and the United States.
The Aran modular mixing system used for producing the RCC in the Philippines is based on well proven technology employed over 25 years ago and still constructing the majority of the RCC pavements in North America today.
The Aran WBS series plant (based on heritage Aran technology) manufactured in Asia, presented Cemex a plant relevant to the commercial environment and capable of delivering accurate material proportioning and mixer performance, critical for RCC.
Cemex are motivated and equipped to expand their business with RCC. Successful construction of RCC pavements demands attention to material selection and gradation, mix handling and logistics, to ensure a densely compacted pavement is achieved.
It is without a doubt, the team at Cemex Philippines have the skills, the commitment and now the equipment to see RCC become a leading construction method in the Philippines.
To learn more about Roller Compacted Concrete and why Cemex chose Aran technology to start their RCC business in the Philippines, get in touch through our contact page.
New Aran WBS300, heritage Aran technology for modern area (image below)
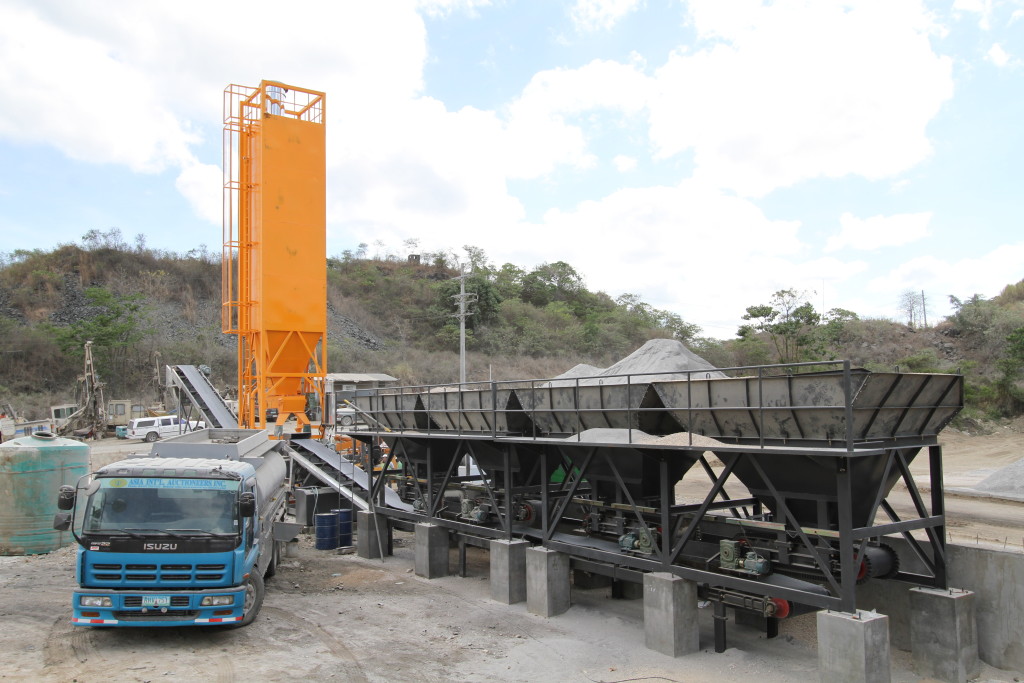
Aran continuous mixer producing RCC
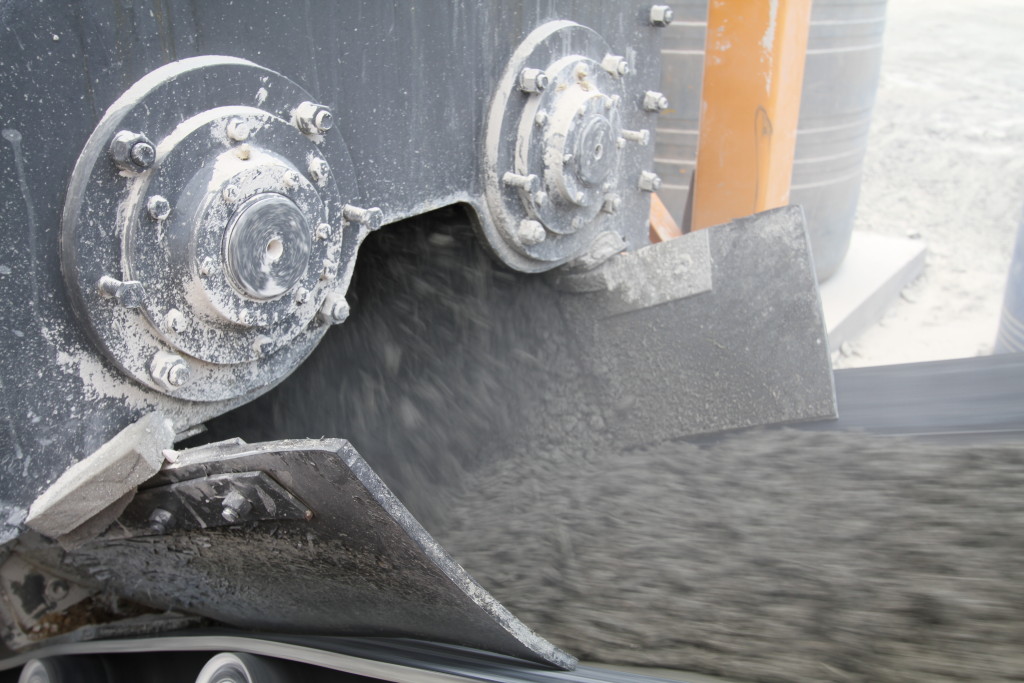
Starting a new run of RCC pavement. Pavement trials in greater Manila, Philippines
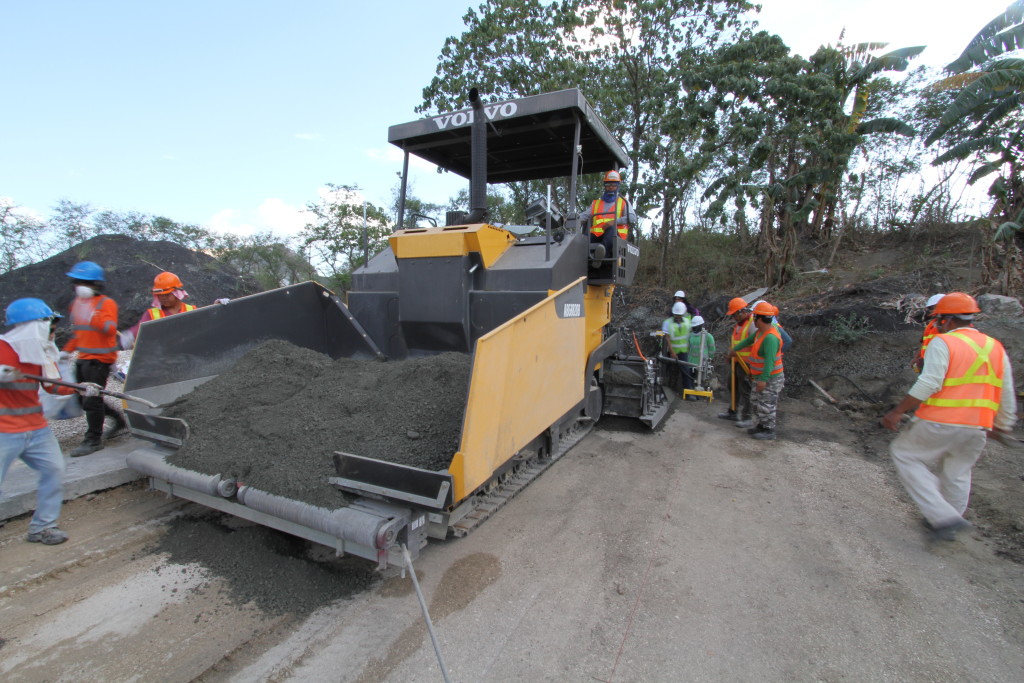
Early RCC Pavement Trial
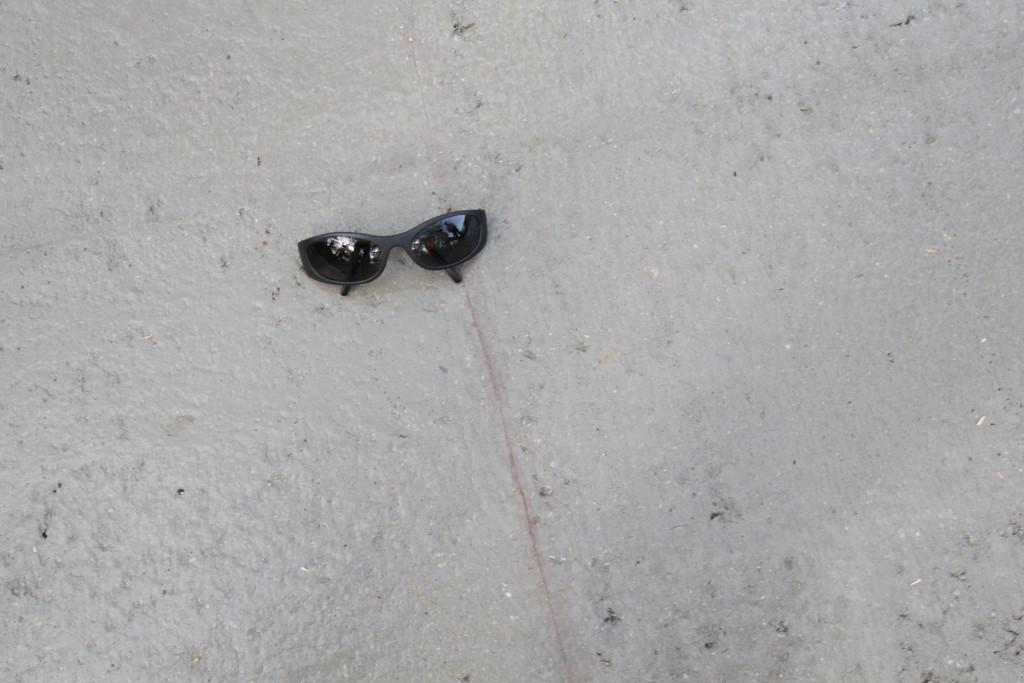
by Shane Dunstan | Mar 13, 2015 | Travel, Upgrading
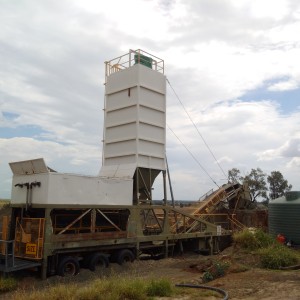
ASR200 located near Roma, QLD, Australia
It is always great to hear how reliable Aran mixing plants are. This week involved a visit an Aran mobile mixing plant operating in the western Queensland Australian town, Roma. This ASR200 has been working hard since it was manufactured in 1984. With a few upgrades along the way, this machine is still producing good quality product at 300 tons per hour. At this site in Roma, it is completing a 300,000 ton project, producing road base for local highway upgrades.
Once this job has finished, we’ll be helping the owner get the plant ready for the next big project. Fortunately there is not much to do, only ensure the silo feed and control systems are in top shape.
If you would like to get your machine performing its best, give us a call. We get a lot of satisfaction seeing old pugmills running like new, if not better!